Virtual vehicle design and architecture planning in the early concept phase
Project completed - Contact: ftm(at)ftm.mw.tum.de
Challenge
Due to a broad variety of use cases and transportation tasks commercial vehicles are characterized by a high degree of variance – contrasted by comparatively low production units. Vehicles are configured very customer-specific, i.e. also the positioning of components is affected profoundly. During the typically long product lifecycle (> 15 years) a lot of innovations and adaptions have to be realized within the existing model range. Furthermore the better part of the vehicles are completed beyond the OEM’s area of influence - numerous body manufactures add their specific bodies (such as tippers, garbage trucks etc.) and attachment parts. Package spaces and interfaces have to be hold available to guaranty a competitive degree of body friendliness. Consequently, high development efforts occur to realize and manage this variance.
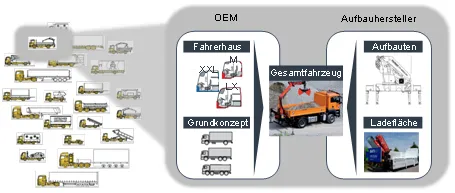
Goal
Systematical architecture and layout planning in the early concept phase helps to define architectural standards that appear as guide rails and avoid uncontrollable change propagation.
With more transparency and stability in the vehicle layout, the operating departments are enabled to realize their component variants more efficiently in terms of a modularization strategy.
In up-to-date industrial practice of commercial vehicle design, there are no integrated design tools available to support the early concept phase focusing on the design of a whole vehicle portfolio.
But for manufactures an economical realization of a broad vehicle portfolio is crucial. This is supported by defining architectural standards harmonizing the different vehicle layouts. The presented approach using abstract and parametrical modeling of components allows for very short computing times for simulating and manipulating different vehicle package configurations.
Assessment metrics for singular vehicle concepts and the whole vehicle portfolio – already in the early concept phase – allow for focusing on costumer-relevant vehicle characteristics and for identifying complex individual vehicles with poor degree of standardization.
Realisation
In order to design commercial vehicle concepts and to create a maximum standardized vehicle portfolio an integrated tool chain is used that is adapted to the early concept phase (see Figure 2).
This tool chain involves a vehicle design environment (“NuKET” implemented in MATLAB, see Figure 2 left-hand) that is used by a conceptual design expert to create a vehicle concept based on customer-relevant complete vehicle characteristics. For configuring a vehicle a component database for about 35 most relevant main components is build. It contains functional as well as geometrical attributes for every component variant to feed the abstract and parametrical CAD parts with data.
All impacts of technical levers on relevant complete vehicle characteristics (driving range, cornering characteristics, axle load potentials etc.) are observable simultaneously.
Afterwards a completed vehicle concept is automatically transferred into a digital CAD mock up (“Architecture-DMU” implemented in CATIA and VBScript). Several DMU functions allow for the analysis of residual package spaces, clashes and promising standards for components’ positioning. Specific spatial validities for components are documented by means of a generic package space decomposition. Architectural standards that could be applied successfully are mandatory for the design of further vehicle concepts. By this a high degree of standardization within the vehicle portfolio is enforced.
The evaluation of vehicle concept characteristics related to a customer profile is done by means of assessment metrics. These are not only applied to individual vehicles but also to the whole vehicle portfolio in order to measure the overall degree of standardization which is crucial for the manufacturer. This assessment provides starting points for retrospectively manipulating particular vehicle concepts in favor of enhanced standardization in the whole portfolio.
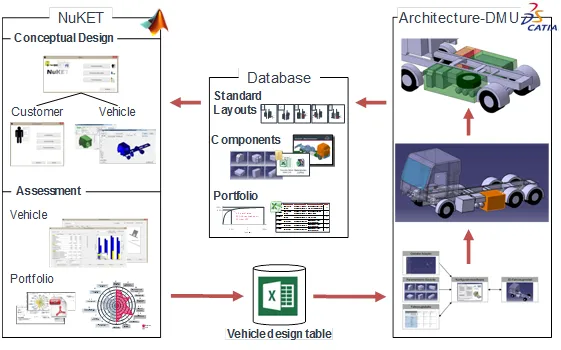