Braking distance optimisation for vehicles with electric drive
Project Completed - Contact: ftm(at)ftm.mw.tum.de
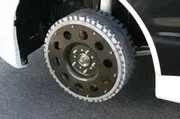
In vehicles with electric motors close to the wheel, it is possible and also necessary to involve these in the ABS control system, thus significantly reducing the stopping distance during emergency braking.
Problem
In drive trains with electric motors arranged close to the wheel - e.g. wheel hub motors - new mass inertia and new couplings of the mass inertia result compared to a conventional drive train. When braking with ABS intervention, this can lead to an extension of the stopping distance, which in turn impairs the safety of passengers and other road users.
Goal
- Determination of the influence of the new inertia ratios on the mode of operation of ABS for different electrical drive topologies (wheel hub motors, axle motor with differential, ...)
- Develop a control concept for the electric motor(s) that compensates for the increase in stopping distance without having to adapt the conventional ABS control.
- Development of strategies to further reduce the stopping distance compared to a conventional vehicle by the electric motor(s) actively supporting the conventional ABS control by the targeted application of torque.
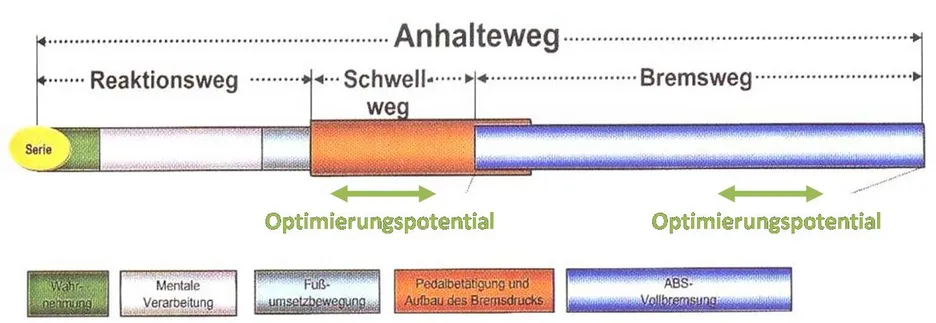
Implementation
- Establishment of a simulation environment in Simulink™ to investigate factors influencing the stopping distance during ABS braking for different electrical drive topologies.
- Establishment of a co-simulation with Adams/Car™ and Simulink™ to develop suitable control strategies for the electric motor(s) and to investigate the influence of dead times on the control.
- Set-up of a "hardware in the loop" simulation with a quarter vehicle on the flat track test bench to validate the simulation results and measure signal propagation times.
- Integration of the concept in a test vehicle